Table Of Content

A strong DFM program should discover multiple opportunities for improving product design. This process often involves closer cooperation between designers and manufacturers, allowing them to identify sources of material wastage. Designers can also work with suppliers to determine the cost and availability of alternative materials. Manufacturability refers to the ease of manufacturing a product, which is highly desirable in DFM. Making a better product at a lower cost is a primary goal in manufacturing, whether for a single part, the entire product, or the assembly process. DFM principles for manufacturability help product designers choose the methods for making a part.
Accelerating new product introduction with Valor NPI
For example, a part that needs to move relative to the rest of the product must be separated. For example, buying aluminum by the plate costs about twice as much as in bar stock costs. Design for Manufacturing (also known as Design For Manufacturability or DFM) is often confused with Design for Assembly, but in reality, they are separate methodologies.
Suppliers
It's 2024! - Aerospace Manufacturing and Design
It's 2024!.
Posted: Mon, 01 Jan 2024 08:00:00 GMT [source]
For example, a product that requires specialized tooling or custom components will be more expensive to produce than a product that uses standard components and tooling. The goal of DFM is to minimize manufacturing costs while ensuring product quality and reliability. This is achieved by designing products that are easy to manufacture and assemble, reducing scrap and rework, and minimizing the time and resources required to bring a product to market. Design for manufacturing (DFM) is important because it can save manufacturing costs and complexity by a large margin while maintaining good product quality. Businesses may reduce material waste, improve production procedures, and boost overall efficiency by designing with ease of manufacture in mind. In addition to lowering costs, this strategy promotes a quicker time to market and increased industry competitiveness.
The 3 Goals of DFM
Yield, a Florida-based company known for its bags, jewelry, and home decor, doesn't claim to produce every item in the U.S. However, all of its wooden furniture is made in St. Augustine, Florida, thanks to the company's own on-site wood-shop. The company, which was founded by Christiane Lemieux, founder of DwellStudio, offers affordable yet customizable furniture.
In particular, it allows engineers to address potential problems in the design phase where they’re less expensive to fix. Design for Manufacturing (DFM) is the process of designing parts, components or products for ease of manufacturing with an end goal of making a better product at a lower cost. The acronym DFMA (Design for Manufacturing and Assembly) is sometimes used interchangeably with DFM. Involving all stakeholders minimizes board spins and iterations, saving the tedious back and forth between designers and manufacturers, and accelerating the time to market and reducing costs. Many promising new avenues for improving manufacturing processes and products are opening up as a result of combining DFM with cutting-edge technologies. DFM methodology is useful in electronics production because it helps optimize component designs for reliability while also improving ease of assembly and production costs.
Materials
Your goal is to choose materials that are available, cost-effective, and suitable for the manufacturing processes. DFM involves several principles and guidelines to optimize the design of a product. The principles may vary based on the industry, product type, and manufacturing processes used. The goal of this case study [6] was to make diesel engines more economically viable by reducing manufacturing and assembly costs.
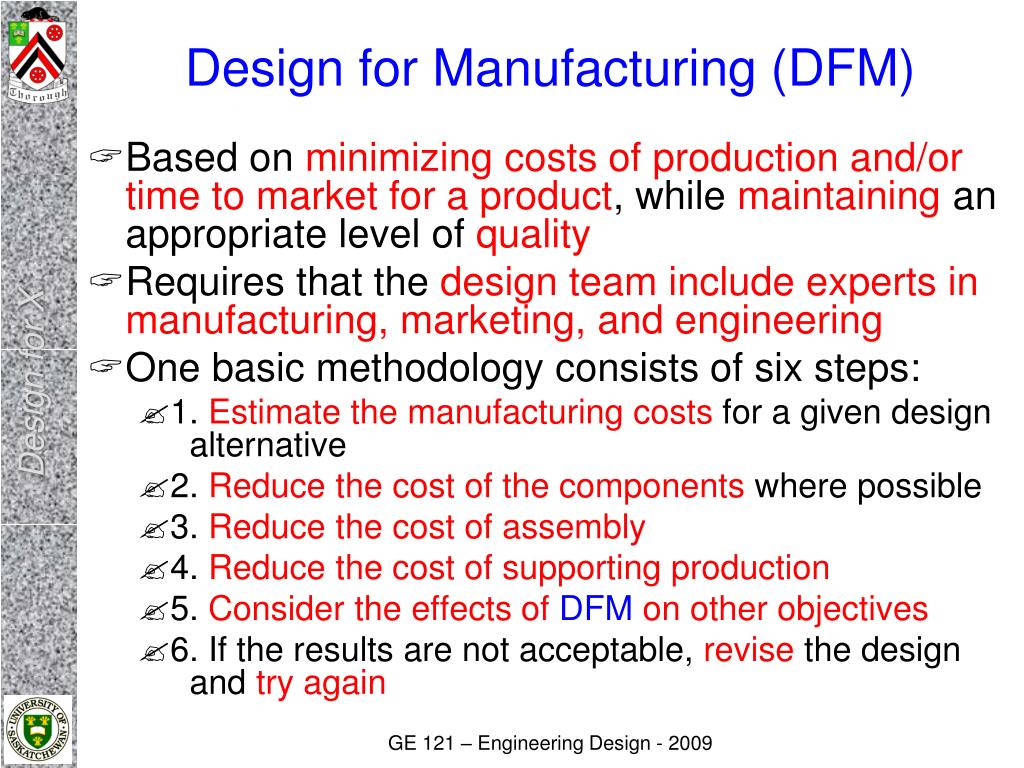
This involves making decisions in the design phase that will simplify the production process, like choosing readily available materials, reducing the number of parts, and considering ease of assembly. By simplifying and optimizing the product design, DFM aims to achieve better manufacturability, leading to improved overall product performance and competitiveness in the market. DFM occurs early in product development, before tooling and the assembly process, when the product is being designed. Doing so will make manufacture less time-consuming, which will reduce cost and increase ease of manufacturing. The exact process of DFM will depend on what product is being designed and produced.

Shorter time to market
We can deliver Design for Manufacturing solutions that will increase your profitability and keep you ahead of the curve. After five short years, the manufacturer’s resistance to DFM caused a decline in sales, quality, and profitability. Reviewing case studies can help you gain a better understanding of the benefits of DFM. These case studies are a great way to compare your results to those of your competitors, learn from industry leaders' mistakes and get ideas for your own projects. Determines the most pressing threats, ranks them in order of severity, and then takes preventative action to minimize downtime, increase safety, and improve dependability. The global pultrusion market is expected to reach $3.0 billion by 2023 with many opportunities for growth in sectors including transportation, construction, consumer goods and...
It focuses on minimising the number of assembly operations and lowering the cost of product assembly. Proto MFG provides a wide range of manufacturing capabilities, including machining and other value-added services for all of your prototyping and production needs. Visit our website to learn more or to request a free, no-obligation quote. A good DFM hopefully concludes by reducing the complexity of the design and satisfying the customer's requirements for price, specification, material and scheduling.
It can be helpful to distinguish design for manufacturability from the closely related idea of a design for assembly. Design for manufacturing (DFM) is significant since it involves creating the process and the product itself. The design influences every aspect of manufacturing, from costs to timeliness to customer pleasure. The specialists can also collaborate with suppliers to understand the limits, allowing them to provide optimum design solutions to improve the setup’s manufacturability in the early phases. As OEMs increasingly outsource manufacturing to distant locations, DFM interventions are increasingly important to guarantee a profitable system. The more complicated your product’s manufacturing process, the more possible mistakes are introduced.
They govern the design of frames to provide simple assembly with varied forks, wheels and components; this broadens component compatibility and flexibility across diverse bike configurations. In cases where customization is required, suppliers can often provide solutions that suit both the design needs and the manufacturing constraints. By working closely with suppliers, businesses can leverage their knowledge to optimize designs for manufacturing, resulting in better quality products, reduced costs, and faster time-to-market. Engaging suppliers early in the design process can significantly enhance the outcomes of DFM.
The design of the manufacturing process for a composite countersink is considered. Attention focuses on the machining of a countersink used in creating stepped holes of diameter 18N9(+0.043) and 22N9(+0.043) mm. Research on the development of manufacturing processes for cutting tools is reviewed.
When designing, specify the loosest tolerance that will serve the function of the component. There are creative ways to engineer components with lower tolerances that still perform as well as ones with higher tolerances. Depending on various types of manufacturing processes there are set guidelines for DFM practices. These DFM guidelines help to precisely define various tolerances, rules and common manufacturing checks related to DFM. Iterations toward more environmentally friendly products decrease operational expenses and increase material savings, customer satisfaction, investor interest and the planet’s health.
This helps eliminate the risk of discovering too late that a part and process will not fit or function as intended. In summary, every manufacturing process has its own set of constraints, but also best practices, and clever tricks for getting the most out of every part for the least cost. Make sure to explore process-specific DFM rules and guidelines and consult contract manufacturers.
No comments:
Post a Comment